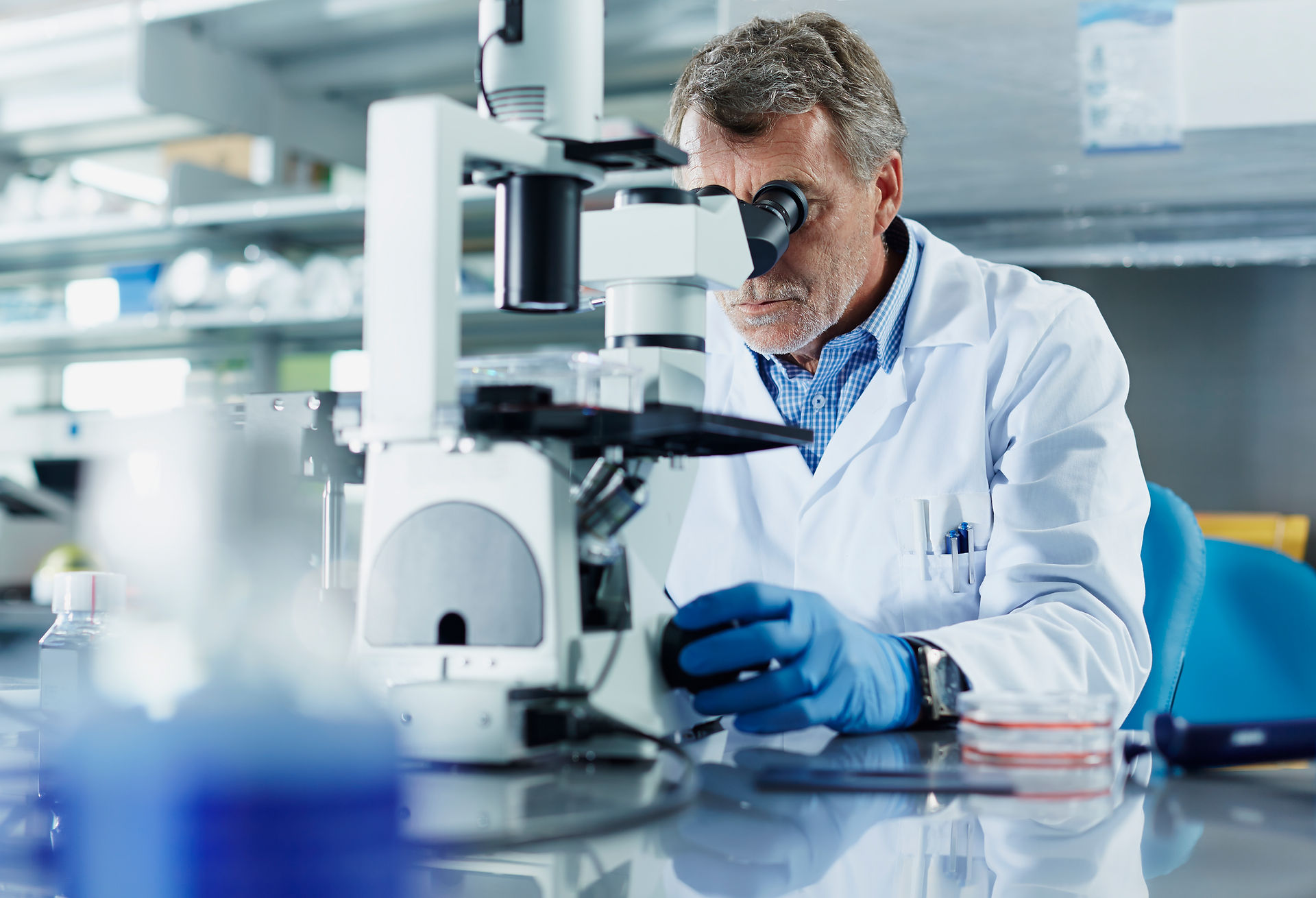
Testing Summary
The components of the RC Baja vehicle were tested and evaluated by Paul Lervick. Specifically suspension coil, the chassis, and the control arms. Each component had a test. The suspension coil had a drop test. The chassis had a center loading test. The control arms had force testing. These tests were done to ensure that each component meets its requirements.
​
There was challenges during each test that were experienced. Most notably, a problem during the chassis deflection test. It was challenging to actually measure the deflection accurately as it was a very minor amount of defletion in a challenging location to measure. Forturnatly, a fellow classmate, Ryan Lafrmanbois, suggested the use of feeler gauges as he ran into a similar problem. This measuring tool solved the problem by enabling accurate measurement in awkward locations.
​
​

Figure 1: Suspension Test Measuring Device In Resting State

Figure 2: Suspension Compressed From 3 Foot Drop
Drop Test
First, the drop test was done to see if the suspension met the requirement of not compressing more than 50% of its free length when dropped from 3 feet. This was done by recording the RC car on the floor when it met the ground in slow motion. There was a measuring device attached to the suspension coil that the slow-motion video would be able to track and gather data on as seen in Figures 1 and 2. The suspension had a maximum compression of 28% and the RC car survived all the drop tests and was fully functioning afterward. The slow-motion videos to capture this data can be seen in Figure 3.
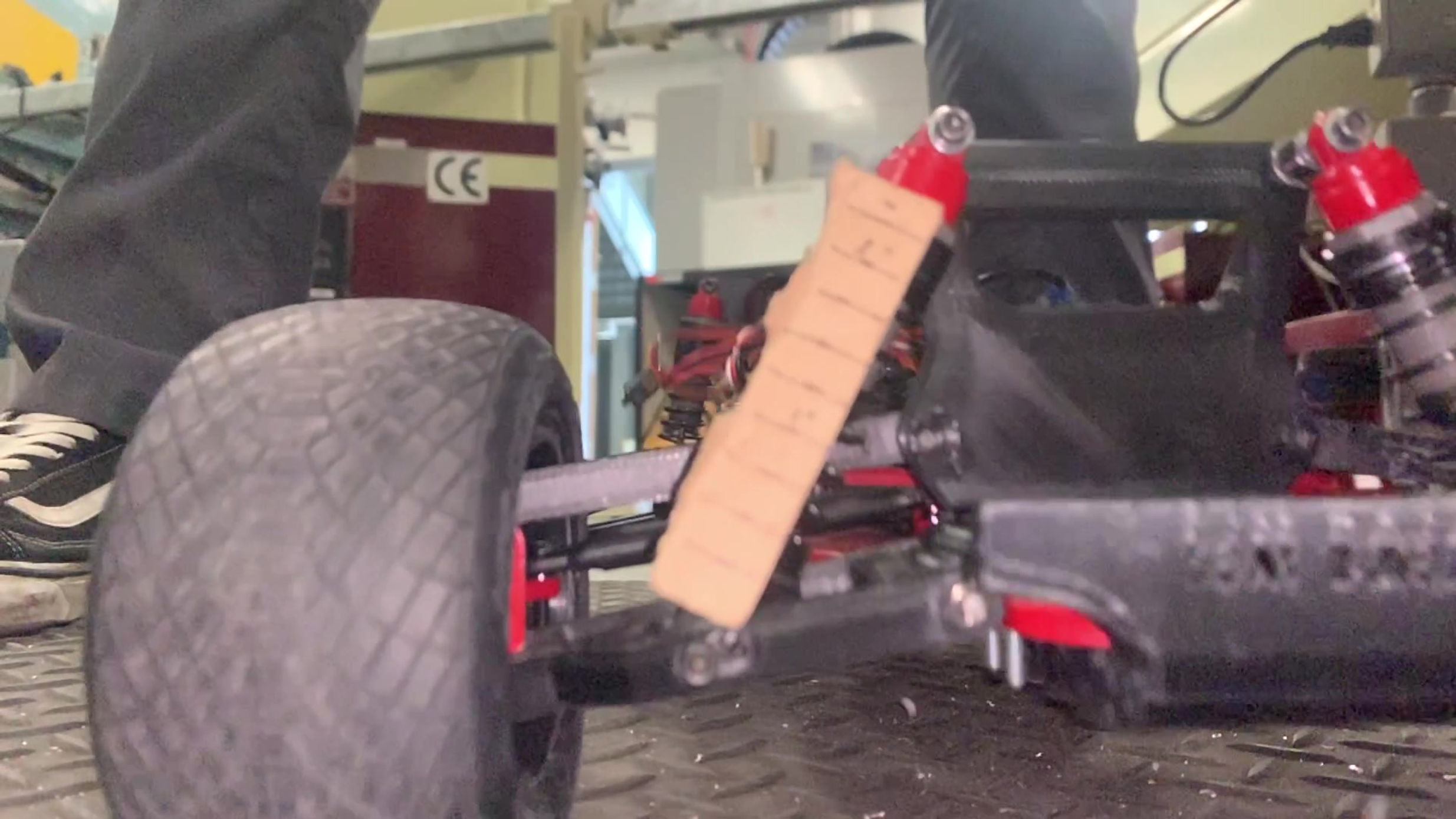
Figure 3: Slowmotion footage of the 3 trials
Chassis Deflection Test

Figure 4: Deflection test setup

Figure 5: Highest deflection load
To meet the requirement for this test, the chassis mustn’t deflect more than 0.05 inches when a 10-pound load was applied to the center. It was found that it took 42.5 pounds of force to reach a deflection of 0.04 inches. So, yes it met the requirement, but why did it exceed it by so much? This is because the 1/8th inch aluminum chassis that was chosen was readily available and easy to manufacture. The Setup of the test can be seen in Figure 4 and the chassis with the max load can be seen in Figure 5. Also, all the data gathered for the test can be seen in Table 1.

Table 1: Deflection Data
Control Arm Deflection Test
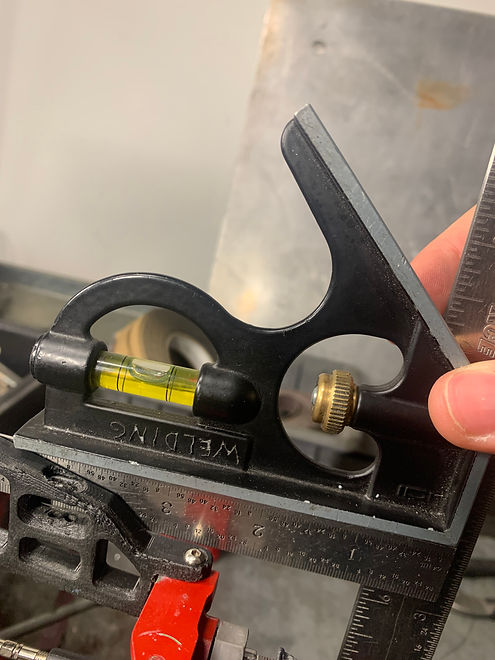
Figure 6: Square edge for taking measurements off of.

Figure 7: Mechanism for applying load to control arm.
To meet the requirement for this test, the control arms couldn't deflect more 0.03 inches when a 10 lb load was applied at the end of the arm. It was found that when a 10 lb load was applied the deflection of the control arm was .026 inches as seen below in Figures 8 and 9. So, the control arm did meet the requirement set for it. Figures 6 and 7 display the set up for the test as see above.

Figure 8: Maximum deflection of control arm.

Figure 9: Control arm with applied load.